What, Why, and How of Flexible Shaft Couplings
The following statements might seem simplified to the point of being naïve. They are not. These statements are very narrowly defined, are common to virtually all precision flexible shaft couplings used in motion systems today, and the basis for most of the detailed technical information in the rest of this web site.
Why Flexible Shaft Couplings
Flexible shaft couplings are used for one reason and one reason only: To preserve the integrity and extend bearing life of the coupled components by flexing, while still transmitting torque.
What Flexible Shaft Couplings Do
Keep in mind that our subject is precision flexible shaft couplings for motion systems and we are largely ignoring power transmission (PT) flexible shaft couplings in this discussion. That being said the purpose of all flexible shaft couplings is this: To accurately transmit torque and rotary position from one shaft to another shaft. The list of things they should not do is just a bit longer and is discussed throughout this web site.
How Flexible shaft couplings work
The simple answer is…there is no simple answer. Designs for flexible shaft couplings are numerous, with some methodologies dating back to the Industrial Revolution. Some of the more common flexible shaft couplings in production today include; bellows coupling, oldham coupling, jaw or spider coupling, and the beam type coupling manufactured by Rocom. There are precious few new or unique designs in the world of flexible shaft couplings. Most of the considerable improvements made recently are due to new methods of manufacturing and modern materials being applied to tried and true designs, some of which are over a century old.
In any given motion control system the forces that act upon the flexible shaft couplings are the same regardless of the design or type, but the introduction of two different flexible shaft couplings with seemingly identical performance criteria can make a radical difference in the overall system performance. Fortunately, the 80/20 principal applies here as follows: if you address the most common issues before your system design is done (the 20%), you will avoid most of the potential problems (the 80%) on the back end of your design.
The Witness Groove™
RoCom Coupling Corp includes a Witness Groove on our flexure beam couplings to help users easily and quickly identify which end of the coupling is the B1 Bore. The Witness Groove is a light groove on the OD of the coupling to aid in the correct orientation during installation.
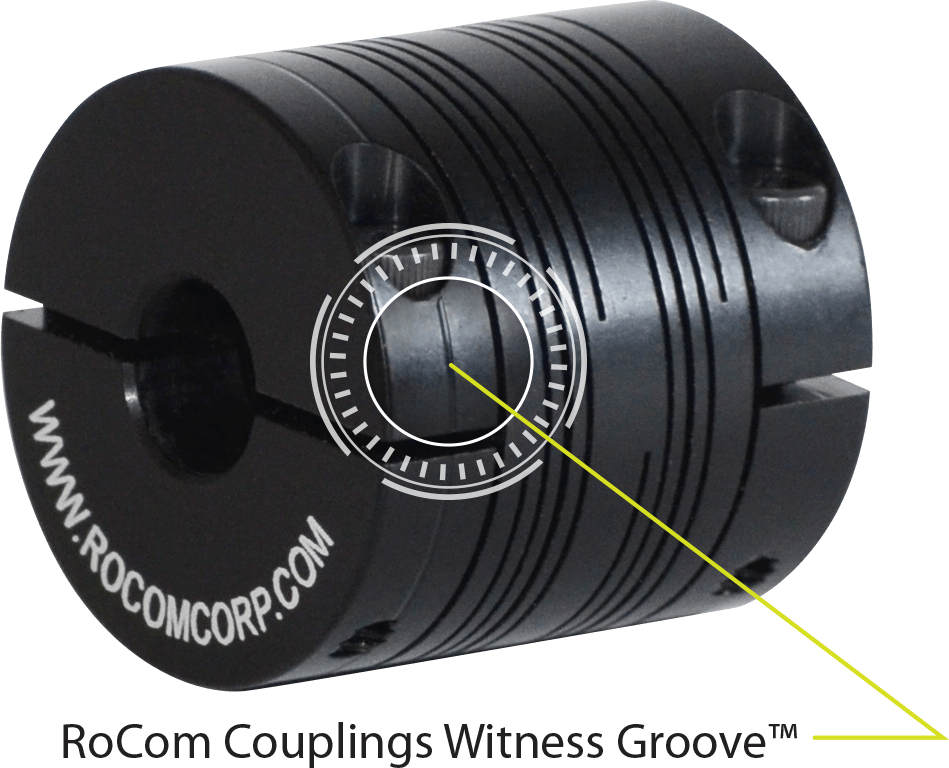